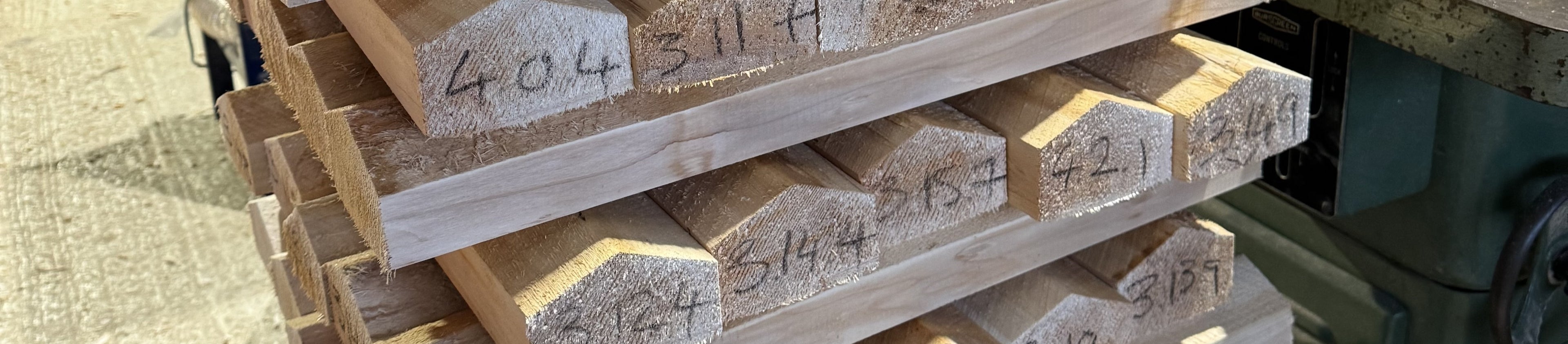
The Cricket Bat Making Process
We pride ourselves on making the highest quality cricket bats, from the highest quality willow, grown exclusively in the UK. While some brands are using Serbian, Kashmir, Dutch, or Australian willow, we are only using English Willow. Though it may take a couple of hours to make a bat, through a combination of machine work and elbow grease, the journey from sapling to shaped, sanded, polished, & stickered cricket bat, starts many years earlier. Kashmir willow difference.
1. Planting. A typical tree takes between 15-20 years to reach maturity. By 'maturity' we mean approximately 60 inches in diameter, or if you were to wrap your arms around the tree, your finger tips would just be touching. Though there are over 90 species of willow that habituate the UK countryside, the most suitable for cricket bat making is Salix Alba Caerulea. Once the sapling, or 'sett' has been planted, given the tree receives adequate care from human intervention, coupled with the correct growing conditions, the longest part of the bat making process has been completed.
2. Felling. Once 'maturity' has been reached, the tree will be cut from the ground, with the main trunk of the tree being the wood we need for bat making. The trunk will then be cut into 29 inch lengths, otherwise known as 'rounds'. From here the rounds are split by a machine into what appears to be a triangle shape, with the point of the triangle coming from the centre of the tree. The timber then enters the milling stage of the process, where after a number of cuts this lump of wood, now resembles what is called a 'cleft'. Each cleft will make one cricket bat, given that are no faults in the wood, while the average tree will produce between 30 and 40 clefts.
3. Drying. The cleft needs to spend months being dried, before it can enter the bat making workshop. The ends are waxed to minimise splitting when the moisture leaves the wood, before being naturally air dried, usually for around 3 months. At this point the cleft enters the kiln, which is a controlled environment aimed to lower the bat moisture content to the optimum percentage for cricket bat making. This number will vary by brand and location, however the general acceptance is between 8-12% in today's UK market.
4. Bat Making. This is where the fun begins, and where the 'cleft' becomes what a cricket player would recognise as a cricket bat. This is also where the OX29 bat making process begins. We receive our willow order, which we receive on pallets, in boxes, in the grades that we have ordered.
The first thing we do is cut the cleft to and oversized width, cuts the ends to an oversized length, and cut the face of the bat to reveal the grains. This is done using a surface planer, rip saw, and spindle moulder. We then regrade this willow into our Players' Grade, Grade 1, Grade 2, Grade 3, and Butterfly, based on the grains, and weight of the clefts. This ensures that our customers receive what they are paying for, within our cricket bat grading criteria. At this point we also check for faults, drying cracks, and current moisture content within the cleft, to ensure no surprises are found later on. Quality control at this point is absolutely vital to avoid wasted time, wasted material, and an end product that is not satisfactory.
Without giving too many of our own secrets away, we then give our bats their first press in the cleft form, splice a handle into the blade, cut the shoulders in, before finally cutting the toe length. This is where the hand work comes in. Using our preferred combination of drawknives, spokeshaves, planes, and rasps, the bat will be shaped before being sanded, polished and bound. The finished bat will then be completed as per the customer's preference re stickers, grip, anti scuff sheet, and knocking in, or be added to stock where the future customer can aesthetically customise the pre made bat. We currently have 9 sticker options, 4 anti scuff sheet options, and dozens of grip options, so choose wisely!
Handcrafted Cricket Bats
Produced in the heart of Oxfordshire
-
Grade 1 Plus, 2.9, Mid-Low Middle - OX29 Handmade #190
Regular price £375.00Regular priceUnit price / per -
Grade 1 Plus, 2.9, Mid-Low Middle - OX29 Handmade #189
Regular price £375.00Regular priceUnit price / per -
Grade 1 Plus, 2.8 Mid-Low Middle - OX29 Handmade #162
Regular price £375.00Regular priceUnit price / per -
Grade 1, 2.7.3, Low Middle - OX29 Handmade #187
Regular price £350.00Regular priceUnit price / perSold out -
Grade 1, 2.7.5 Mid - Low Middle - OX29 Handmade #158
Regular price £325.00Regular priceUnit price / per -
Grade 1, 2.6.9 Low Middle - OX29 Handmade #156
Regular price £325.00Regular priceUnit price / per
OX29 Bat Doctor